Laser Beam Profiler
Laser Beam Profiler is an instrument that measures the beam diameter and spatial intensity distribution of a laser. The beam diameter and spatial intensity distribution are laser characteristics that describe how the beam will behave.
For example, even if a laser has the same intensity and beam diameter, if the spatial intensity distribution is different, the focusing characteristics will change, and the same behavior will not be obtained. In addition, even if the laser cavity is rigorously designed, it is affected by manufacturing errors in the optical elements and the surrounding environment such as temperature. Therefore, it is difficult to accurately predict the beam characteristics to be obtained.
For this reason, it is important to measure the actual beam characteristics in laser beam applications.
A Laser Beam Profiler is used to measure the beam characteristics.
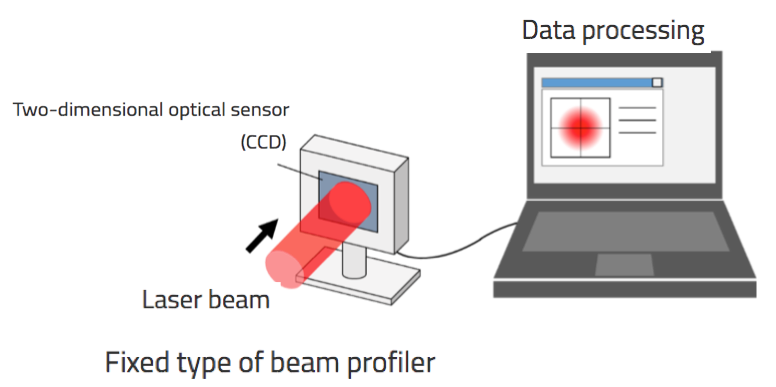
Laser Beam Profiler / Kokyo products features
- Beam diameter 2 μm 〜 800 mm measurable
- Wavelength 190 nm 〜 18 μm measurable
- Customization available on both software and hardware
- Laser power 0.001W/m2~ 10 kW/m2 measurable
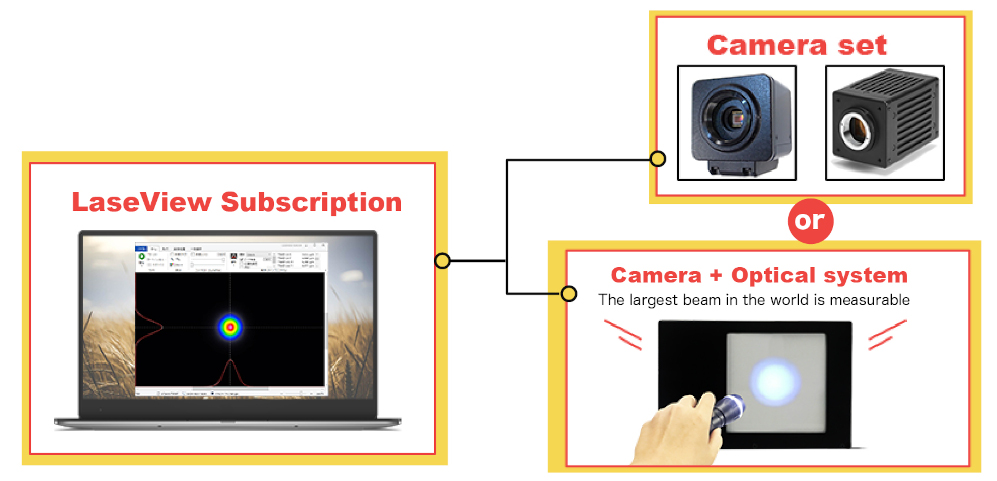
Laser Beam Profiler / Kokyo products line-up
Software
Commercially sold low-cost camera is available as Laser Beam Profiler. Multiple cameras can be connected to Single software.
Camera set
Most suitable camera is selected for each condition, such as laser wavelength, beam diameter and pulse/CW.
Camera + optical system
Beam diameter (2 μm 〜 800 mm), wavelength (190 nm〜18 μm) and power (〜1 kW) are measurable.
Laser Beam Profiler, which can measure the largest beam in the world is also available.
Laser Beam Profiler selection / wavelength x beam diameter
Selection by wavelength and beam diameter | wavelength | |||||
---|---|---|---|---|---|---|
190 – 400 nm | 400 – 1100 nm | 950 – 1700 nm (NIR) | 1 – 18 μm (MIR) | |||
Beam diameter | 2 μm~ 100 μm 5 μm~ 100 μm (NIR) |
Micro beam diameter measurement optical system set + camera LaseView-CA-DUV-BE |
Micro beam diameter measurement optical system set + camera LaseView-CA50-NCG-BE |
Micro beam diameter measurement optical system set + camera LaseView-CA-SWIR-BE |
Custom correspondence | |
30 μm~ 5 mm 200 μm~ 5 mm (NIR) 90 μm~ 12 mm (MIR) |
Femtosecond pulse or condensed light |
Camera set LaseView-CA50-NCG |
Camera set LaseView-CA-SWIR |
Camera set LaseView-CA-MIR |
||
Parallel light | Custom correspondence | ー | ||||
5 mm ~ 10 mm | Laser Beam Profiler with UV converter LaseView-SRC-DUV *corresponding to 200 – 390 nm |
LaseView with Screen Reduction Converter for LED measurement LaseView-SRC-LED *corresponding to 400 – 800nm / 800 – 1000nm, Please indicate the wavelength you require. |
ー | ー | ||
1 mm ~ 50 mm 3 mm ~ 50 mm (NIR) |
ー | Laser Beam Profiler for large diameter and high-power LaseView-LHB-25 |
Laser Beam Profiler for large diameter and high-power(NIR) LaseView-LHB-NIR |
ー | ||
Laser Beam Profiler for large diameter and high-power LaseView-LHB |
||||||
– | Laser Beam Profiler for large diameter and high-power (High heat-resistant type, ~100 kW/cm2) LaseView-LHB-UHP |
ー | ー | |||
Laser Beam Profiler for large diameter and high-power (Wide wavelength) LaseView-LHB-VISNIR |
ー | |||||
1 m ~ 100 mm 3 mm ~ 100 mm (NIR) |
ー | Laser Beam Profiler for large diameter and high-power LaseView-LHB-100 |
Laser Beam Profiler for large diameter and high-power(NIR) LaseView-LHB-100-NIR |
ー | ||
Laser Beam Profiler for large diameter and high-power(Wide angle of incidence version, ~±70°) LaseView-LHB-100-WA |
||||||
ー | Laser Beam Profiler for large diameter and high-power (Wide wavelength) LaseView-LHB-100-VISNIR |
ー | ||||
1 mm ~ 800 mm | ー | Laser Beam Profiler for large diameter and high-power LaseView-LHB-200 |
ー | ー | ||
Laser Beam Profiler for large diameter and high-power(Wide wavelengths) LaseView-LHB-200-VISNIR-GigE |
||||||
Laser Beam Profiler for large diameter and high-power(Wide wavelengths) LaseView-800 |
Laser Beam Profiler selection / wavelength x power
Selection by wavelength and power | wavelength | ||||
---|---|---|---|---|---|
190 – 400 nm | 400 – 1100 nm | 1060 – 1080 nm | 950 – 1700 nm (NIR) | ||
power | ー | Laser Beam Profiler with M2 platform software LaseView |
|||
< 100 mW | +ND filter set(NDFS-CA50) | ||||
< 1 W< 10 W | +Attenuating optics set with beam splitter | ||||
< 100 W | +Attenuation optics set with double beam splitter | ||||
< 10 W | ー | Laser Beam Profiler for large diameter and high-power LaseView-LHB-25 |
Laser Beam Profiler for large diameter and high-power(NIR) LaseView-LHB-NIR |
||
Laser Beam Profiler for large diameter and high-power LaseView-LHB |
|||||
< 600 W | ー | ー | Laser Beam Profiler for 600W fiber laser LaseView-600FL |
ー | |
< 1k W | ー | ー | Contact us | ー |
Laser Beam Profiler / Type and Pros & Cons
Fixed Laser Beam Profiler system with CCD camera is adopted on Kokyo’s products.
Here are advantages and disadvantages between scanning Laser Beam Profiler system and fixed Laser Beam Profiler’s one.
Advantage | Disadvantage | |
---|---|---|
Fixed Laser Beam Profiler ・CCD camera type |
|
※ Kokyo’s Laser Beam Profiler is low-cost and can measure large beam diameter |
Scanning Laser Beam Profiler ・Pinhole type ・Slit type ・Knife Edge type |
|
|
Laser Beam Profiler of Kokyo / Merit & Advantage
Commercially sold CCD camera or CMOS camera is available on Kokyo’s Laser Beam Profiler and so,
low-cost and practical beam measuring system can be easily structured.
Also, due to low-cost cameras, beam monitoring system with multiple cameras can be structured with low-cost on Kokyo’s system.
Kokyo’s product | Conventional one | |
---|---|---|
Customization | ◎ | ✕ |
Sales in combination | 1. Software only 2. Software and camera 3. Software, camera and optical system |
Software and camera only |
CCD camera by third company | ◎ | ✕ |
M2 beam quality measuring function |
◎ (standard installation with software) |
✕ (separate purchase) |
Measurable minimum beam diameter |
2 μm – | 30 μm – |
Measurable maximum beam diameter |
– 200 mm | – 24 mm |
Measurable maximum power |
~ 600 W | ? |
Language | Same as language on PC (English description is shown if it is English PC. Japanese is shown if it is Japanese PC) |
English |
Laser Beam Profiler of Kokyo / Customer’s Reviews
- Camera is inexpensive, so don’t worry about breaking it.
- Camera can be used as disposable.
- Easy to prepare.
- The software is intuitive and easy to use.
- Inexpensive.
- M2 beam quality measurement is included as a standard feature, which is very nice.
- The evaluation results showed that the software works as expected, so we have just ordered the software. (used the evaluation version before purchasing)
- Kokyo’s Laser Beam Profiler has been installed into our device and we find it very useful.
- Just Irradiating large diameter laser light makes easy measurement.
- This is only product/device to be able to evaluate laser from LiDAR and we find it vey helpful
Laser Beam Profiler of Kokyo / Our customers
- Leibniz University Hannover
- LMU Munich
- University of Vienna
- Victoria University of Wellington
- Institute of Atomic and Molecular Sciences Academia Sinica
- University of Southampton(Britain)
- Helmholtz-Zentrum Dresden-Rossendorf (HZDR, Germany)
- Institute of Physics AS CR, v.v.i. (Czech Republic)
- Jet Propulsion Laboratory, NASA
- Osaka University
- Kyushu University
- Kyoto University
- Kyoto Institute of Technology
- Shinshu University
- Nagoya University
- University of Electro-Communications
- The University of Tokyo
- Tokyo Institute of Technology
- Sophia University
- The Graduate University for the Creation of New Photonics Industries
- Hiroshima University
- University of Fukui
- Yamagata University
- University of the Ryukyus
- Utsunomiya University
- Saga University
- Japan Coast Guard (JCG)
- RIKEN
- National Institute for Fusion Science
- National Institute for Materials Science
- Japan Synchrotron Radiation Research Institute
- National Institute of Laser Science and Technology
- National Institute of Advanced Industrial Science and Technology (AIST)
- Japan Atomic Energy Agency
- National Institute of Information and Communications Technology
- Japan Aerospace Exploration Agency
- Quantum Science and Technology Research Organization
- National Astronomical Observatory of Japan (NAOJ)
- Japan Coast Guard Headquarters
- Manufacturer of optical systems for information equipment and industrial applications
- Manufacturer of optical product research and development
- Israeli defense equipment manufacturer
- Major electronics manufacturer
- Major manufacturing manufacturer
- Leading manufacturer of measuring instruments
- Leading manufacturer of electronic measuring instruments
- Manufacturer of optical products
- Taiwanese electronics manufacturer
- Korean general home appliance manufacturer
- Other domestic and foreign private companies
Laser Beam Profiler of Kokyo / Usage videos
“Introduction of the large diameter Laser Beam Profiler (LaseView-LHB) for evaluation of laser scanners, various light sources”
“Introduction of Laseview-LHB”
“Usage example of Laseview-LHB”
“Selection of products”
Laser Beam Profiler of Kokyo / Distributors
All Kokyo products are available directly from Kokyo, Inc. We accepts orders from all domestic and international customers.
To place an order, please write to us. Feel free to contact us with pre-purchase questions. We look forward to hearing from you.
info@symphotony.com
Or purchase from one of our distributers.
We have distribution channels of “Laser Beam Profiler LaseView series” as below.
Korea
Dylan Hong
CTL GLOBAL
327, 5, Beobwon-ro 4-gil, Songpa-gu, Seoul, Korea
Tel : +82 070 7779-4500
Fax : +82 42 367 4300
yshong@ctloptics.com
ww.youtube.com/channel/UCsovG44FeikIp-zYfLZP3uw
ctl.imweb.me
Germany
Bernd Dietz
Geschäftsführer / Managing Director
nortus Optronic GmbH
In den Niederwiesen 4a
D-76744 Wörth am Rhein
Tel : +49-7271-12990-0
Fax : +49-7271-12990-19
info@nortus-optronic.com
www.nortus-optronic.de